大型から小物まで
機械加工は竹沢精機にお任せください
大型機械加工はもちろん、小物加工、板金、塗装、めっき、その他組立など、ほとんどの加工が可能です。資材調達から仕上げまで、一貫生産体制でお客様の図面を製品化いたします。
私たちには図面を形にする力があります
加工から仕上げ、組立まで一貫生産体制で図面を製品化
図面支給と構想形式、竹沢精機へのご発注の流れ
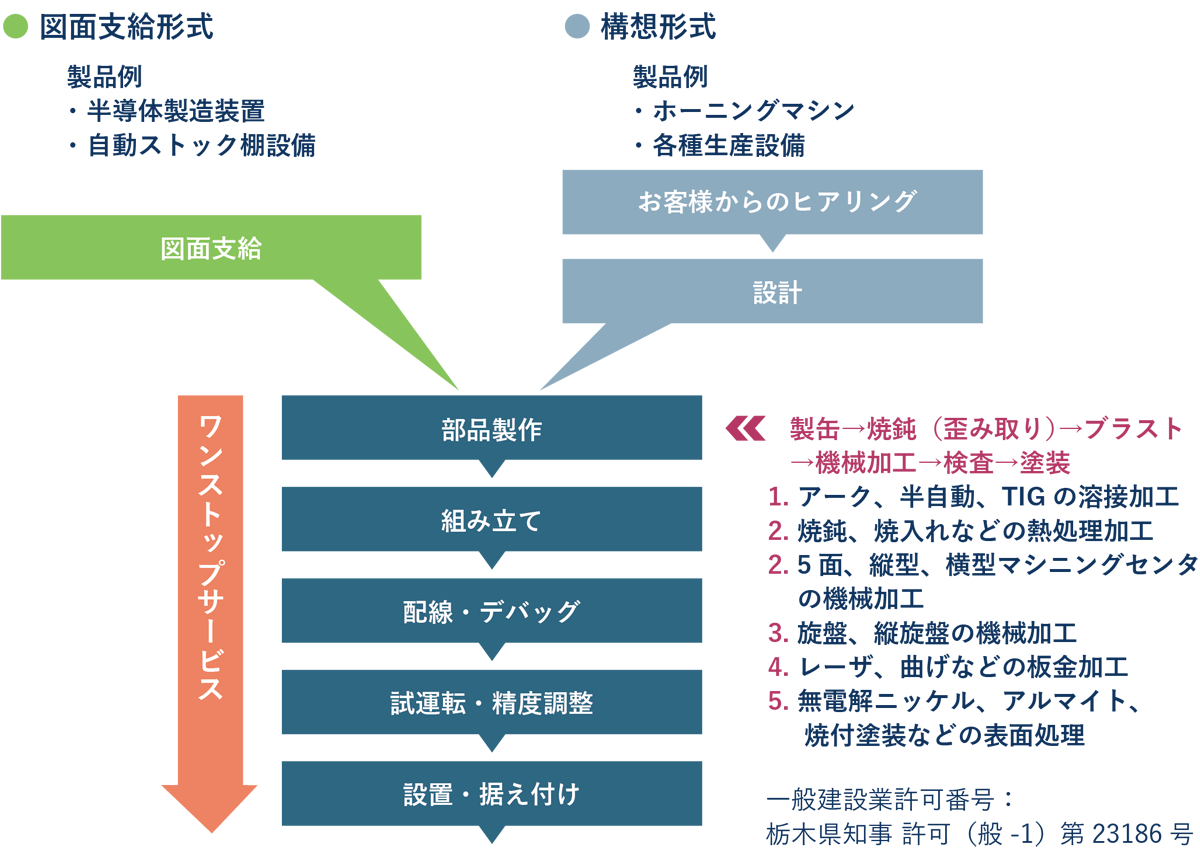
竹沢精機の精機事業の受注形式は2種類あります。一つ目は、お客様より図面をご支給頂き部品製作、更に塗装・組立・電装・試運転・現地据付まで一連で行う図面支給形式。もう一つは、さらに上流からでお客様ニーズを吸収し設備構想~そして図面化をして、その後に前者と同じく部品製作~現地据付と範囲を拡大して実施する構想形式です。一般建設業許可も取得済みですので制限なく工事ができます。
当社は長年の経験から常に学び続け、お客様にご満足いただける装置を提供するために、熟練度を要する加工及び、装置の特性を熟知するからこそできる組み立て技術を磨いてまいりました。
機械加工、機器開発などをご検討の際には、ぜひ当社へご相談ください。
納入先例
【図面支給形式】
半導体部品メーカ、レーザ加工機付帯設備メーカなど
【構想形式】
自動車部品メーカ、電気部品メーカ、建設機械メーカ、その他各種産業機械など
竹沢精機の強み
- 自達による小型部品から大型部品に至るまで製作が可能です
- TAKEZAWAネットワークによる各種処理(熱処理、メッキ、塗装など)、そして経験の豊富な組立技術へと一連で行います
- お客様の要求に基づいた専用設計、そしてコストを考慮した設計、加工技術があります
- 設計技術を伴った現地据付ノウハウによる充実したアフターサービス
- 大型機械加工が可能
テーブルサイズ3000×8000大型の五面加工機を保有しておりますので、他社では加工できない大きさのものがあればぜひご相談ください。鋳物加工も対応できます
機械加工事例
ソーラパネル成型用の大型真空容器の製作
【機械加工メーカI社様】
<要求精度>
幅:2500mm
長さ:4300mm
高さ:700mm
平坦度:0.1mm
真空度:130Pa以下
(1気圧は約101000Pa)
真空状態でソーラパネルをラミネート加工するための大型の真空容器を製作して欲しいというご依頼がありました。このときは、製品の試作品開発から量産までお引受けいたしました。
真空容器といっても長さ4.3m、幅2.5mという巨大な容器の製作でした。これだけの大きさの場合、従来では問題にならなかったことが大きな問題を引き起こします。容器の固定方法によるわずかな歪み、溶接面のわずかなピンホールなどが影響し、真空度を維持することを困難にします。
依頼があった段階で、要求精度以外に決定されていたものがなく、挑戦的な仕事になりました。
製品の材質、加工法、加工順序の研究を丹念に行った結果、真空度を損なうピンホールの発生を抑え、大型加工物でも寸法が狂わない溶接技術および、冶具の開発に成功し、安定した量産体制を確立することができました。
大型加工が必要なリコイラの製作
【機械加工メーカF社様】
<要求精度>
長さ:600mm
直径:760mm
勾配:±5/100
大型加工が必要なリコイラを製作して欲しいというご依頼でした。
リコイラとは、鋼板を巻きつける芯になる部品です。リコイラに鋼板を巻きつけた後、リコイラの径を収縮させて、鋼板を抜き取ります。リコイラの外周部分は4つの部品からできており、この部品を正確に連動させることで、リコイラの径を収縮させます。このため、4つの部品を高精度に製作しなければ、鋼板からリコイラをスムーズに抜き取ることができません。
大型部品の加工は、通常の機械加工とは異なり、ワークを大きな冶具で固定することができません。そのため、ワークが振動し、精度を出すことが困難になります。
竹沢精機では、大型機械加工の研究を行い、独自の加工冶具を開発することによって、お客様の要求精度にお応えすことができました。
竹沢精機が教えるコストを下げる設計のコツ
設計者として図面を理解し、職人として加工工程をデザインする竹沢精機は、お客様へのコストダウン提案が可能です。加工現場の視点から図面を考えると、コストダウンの方法が見えてきます。コストのかからない合理的な加工は早さを生み出します。これまで竹沢精機のご提案は、多くのお客様の支持を得てまいりました。
ここでは竹沢精機が今まで行ったご提案の一部をご紹介いたします。御社の図面はまだまだコストダウンできるはずです。
御社も是非一度、竹沢精機にご相談ください。
その1:資材の販売系列を考慮する
軸物を加工する際、丸材を購入します。軸の径は設計仕様に応じて決定されますが、この際素材となる丸材の販売系列を考慮して設計を行うと、コストを削減することができます。
一般に丸材はφ100以上の場合、10mm刻みで販売されています。仮にφ100の軸を設計した場合、購入する素材は削り代があるためφ110となります。この際、直径にして10mmを削ることになります。もし、軸の設計がφ98でも許されるなら購入する素材はφ100で済むのです。削り代は2mmもあれば十分です。これにより、素材の購入費用と切削時間を削減することができ、コストを抑えることができます。
わずかな違いに思われるかもしれませんが、この素材のムダと切削時間の削減だけで15%近くもコストダウンになる場合もあるのです。
その2:組立工程と要求精度を考える
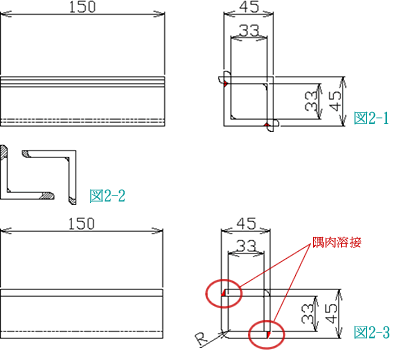
次に図2-1のような四角い形状の筒を製作する事例についてご紹介いたします。当初の図面通り正確に製作するためには、図2-2の等辺山形鋼t6×50×50を必要寸法に機械加工した後、溶接することになります。角が90°に指定されているためこのような製作方法をとります。ここで仮に、90°ではなくR2程度でも許されるならばコストダウンを図る方法があります。もう一方の図2-3のように、板金加工でアングル材を製作し、2ヶ所を溶接するのです。
さらに溶接を隅肉溶接に変更すれば、開先加工も省略することができ、さらなるコストダウンにつながります。このの事例では15%のコストダウンが実現できました。当然、加工時間も短縮されています。30分の工程が5分で完了し、約80%の大幅な短縮となりました。組立工程を要求精度に応じて最適化することで、大きなコストダウンが可能になるのです。
その3:全体最適を図って低コスト化、短納期化を行う
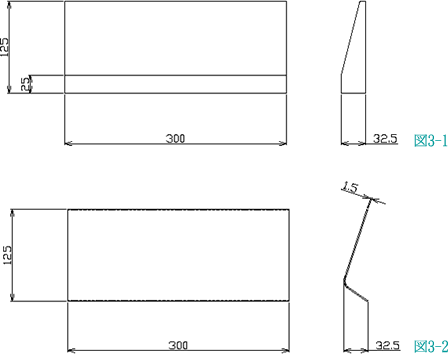
この図は、別の部品を組み付ける際のガイドが設けられた製品の製作事例です。
当初の図面には図3-1のようなガイドを多数設けるよう指示されていました。この場合、切削によりガイドを製作することになります。図3-1のような形状は切削加工でしか作ることができないのです。このガイドを削り出すには厚い板材からガイドの部分以外を削り取ることになるので、素材と切削時間が多く必要となります。しかしこの部分はただのガイドで、それほど精度が要求されるものではありませんでした。
ならば、もっとコストの安い加工方法がとれないか検討の余地があります。
一般に最もコストの安い金属加工は板金加工です。そこで、もう一方の図3-2のように材料の一部を曲げ、ガイドとすることを、ご提案いたしました。機能的にはこれで十分です。もともとこの製品は加工工程の大半が板金加工でした。そのためこのご提案は、前工程として必要になる機械加工を省略し、板金加工に工程を集約するという意味もありました。材料だけでなく工程も合理化することで、さらにコストダウンを行ったのです。たったこれだけのことですが、材料費が約1/5、加工費が約1/2になり、全体で30%ものコストダウンが実現でき、製造時間に関しても24時間の短縮となりました。
要求精度を満たしつつ、合理的な加工方法を選択することが、素材や、加工時間にも大きく影響し、全体のコストを大きく引き下げることは意外と多いのです。